1. Why Does Choosing the Right Dry Wet Vacuum Cleaner Manufacturer Matter?
Selecting a reliable manufacturer for dry wet vacuum cleaners directly impacts product quality, safety, and long-term value. A trusted manufacturer ensures:
- Consistent Performance: High-grade materials and precision engineering prevent leaks or motor failures.
- Compliance with Safety Standards: Proper certifications (e.g., UL, CE) reduce risks of electrical hazards.
- Cost Efficiency: Streamlined production processes lower defects, minimizing repair/replacement costs.
- Innovation Support: Established manufacturers invest in R&D to improve suction power, filtration, and durability.
For commercial buyers, partnering with a reputable brand like ZEK ensures scalable solutions tailored to industrial needs, such as heavy-duty motors or chemical-resistant tanks.
2. What Key Features Should You Prioritize in Dry Wet Vacuum Cleaners?
Focus on these critical features when evaluating manufacturers:
-
Motor Type:
- Brushless Motors: Longer lifespan, quieter operation (e.g., ZEK’s patented VortexDrive™).
- HP Ratings: Match horsepower to your usage (e.g., 5HP for construction debris).
-
Filtration System:
- HEPA filters for allergen containment.
- Automatic filter-cleaning mechanisms.
-
Tank Capacity & Material:
- Stainless steel or polypropylene tanks resist corrosion.
- 10–20L tanks ideal for home use; 30L+ for commercial jobs.
-
Accessories:
- Look for crevice tools, wet/dry nozzles, and blower functions.
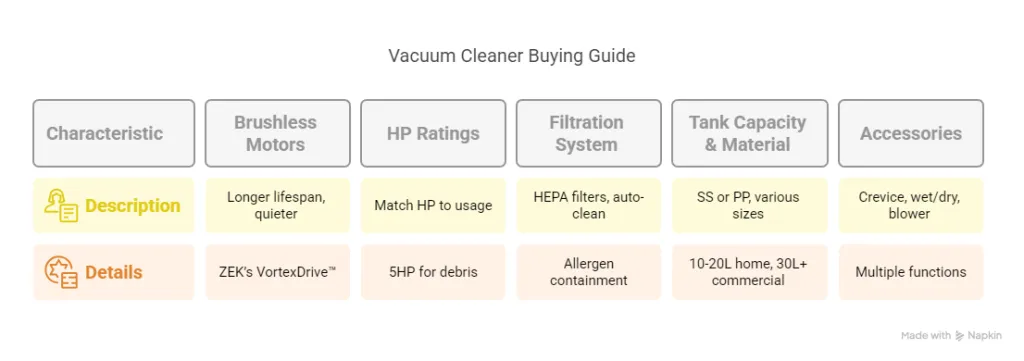
3. How to Evaluate a Manufacturer’s Experience and Reputation
Follow these steps to assess credibility:
Step 1: Check Company History
- Verify years in business (ZEK has 15+ years in vacuum tech).
- Review case studies (e.g., partnerships with hospitality or automotive industries).
Step 2: Analyze Customer Feedback
- Search for third-party reviews on platforms like Trustpilot.
- Ask for client references to confirm after-sales support quality.
Step 3: Investigate Industry Recognition
- Awards (e.g., Red Dot Design) or patents indicate innovation commitment.
4. What Certifications and Compliance Standards Are Non-Negotiable?
Reputable manufacturers must meet these certifications:
- UL Certification: Ensures electrical safety (mandatory in North America).
- CE Marking: Complies with EU health/environmental standards.
- RoHS Compliance: Restricts hazardous substances like lead.
- ISO 9001: Validates quality management systems.
ZEK’s dry wet vacuums exceed these standards, with additional IPX4 water resistance ratings for wet environments.
5. How to Assess Manufacturing Technology and Innovation
Technology Checklist:
- Automated Production Lines: Reduce human error (e.g., ZEK’s AI-driven assembly).
- Testing Protocols: In-house pressure tests, leakage checks, and noise audits.
- Sustainability Practices: Energy-efficient manufacturing or recyclable packaging.
Ask Manufacturers These Questions:
- “Do you offer custom engineering for specific applications?”
- “What percentage of revenue is reinvested in R&D?” (ZEK allocates 12% annually.)
6. Why Balancing Cost and Quality is Critical When Choosing a Manufacturer
Selecting a manufacturer based solely on price often leads to compromised durability or safety. Here’s how to strike the right balance:
- Avoid Cheap Traps: Low-cost manufacturers may use substandard plastics or weak motors, increasing long-term repair costs.
-
Evaluate Total Cost of Ownership (TCO):
- Compare warranty terms (e.g., ZEK offers 3-year warranties vs. industry-standard 1 year).
- Factor in energy efficiency (e.g., ZEK’s brushless motors reduce electricity costs by 15%).
- Request Sample Testing: Assess suction power, leak resistance, and noise levels across price tiers.
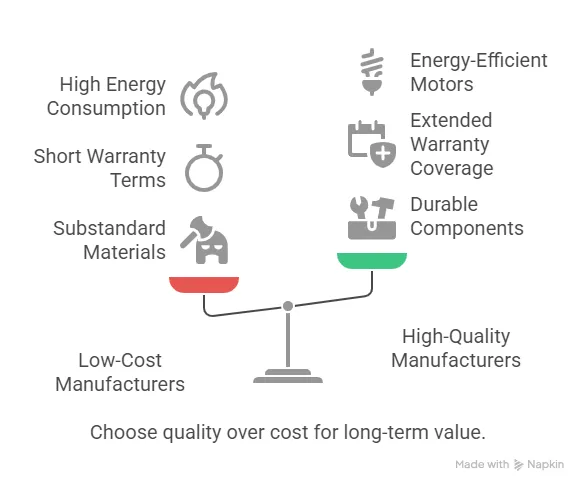
ZEK uses aerospace-grade polymers and precision-molded parts to ensure longevity without inflated pricing.
7. How to Evaluate Customer Support and After-Sales Service
Reliable post-purchase support minimizes downtime. Follow these steps:
Step 1: Verify Service Channels
- 24/7 technical support (ZEK provides live chat, email, and regional hotlines).
- Availability of local repair centers or authorized partners.
Step 2: Check Spare Parts Inventory
- Manufacturers like ZEK stock critical components (motors, filters) for 10+ years.
Step 3: Review Service-Level Agreements (SLAs)
- Look for guaranteed response times (e.g., 4-hour emergency support for commercial clients).
ZEK’s ProCare program includes free training sessions and expedited replacement for faulty units.
8. What Production Capacity and Lead Time Mean for Your Business
High-volume buyers must prioritize manufacturers with scalable operations:
-
Ask These Questions:
- “What’s your monthly output?” (ZEK produces 50,000+ units monthly.)
- “Can you handle rush orders without quality compromises?”
-
Red Flags:
- Overly short lead times (may indicate poor quality control).
- No transparent supply chain maps.
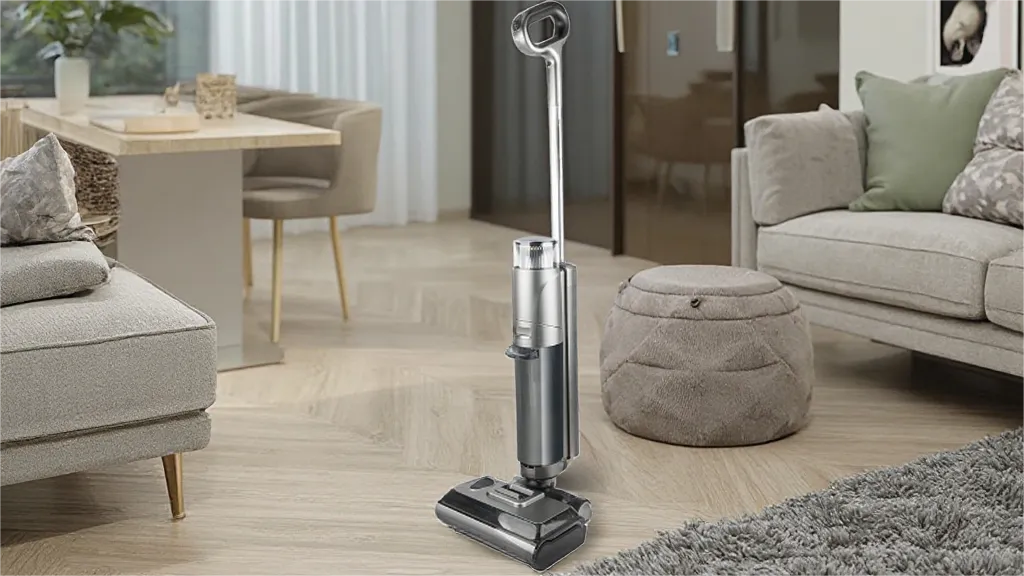
ZEK’s vertically integrated factories and AI-driven logistics ensure 30-day delivery for bulk orders, even with custom specs.
9. Why Customization Options Matter in Dry Wet Vacuum Cleaners
Off-the-shelf models rarely meet niche industrial needs. Prioritize manufacturers offering:
-
Hardware Customizations:
- Tank shapes/sizes for tight spaces.
- Explosion-proof motors for hazardous environments.
-
Software Adaptations:
- IoT-enabled usage tracking (ZEK’s SmartVac™ system).
- Adjustable suction presets.
How to Request Custom Solutions:
- Share application details (e.g., cleaning chemical types).
- Review 3D prototypes.
- Conduct onsite testing.
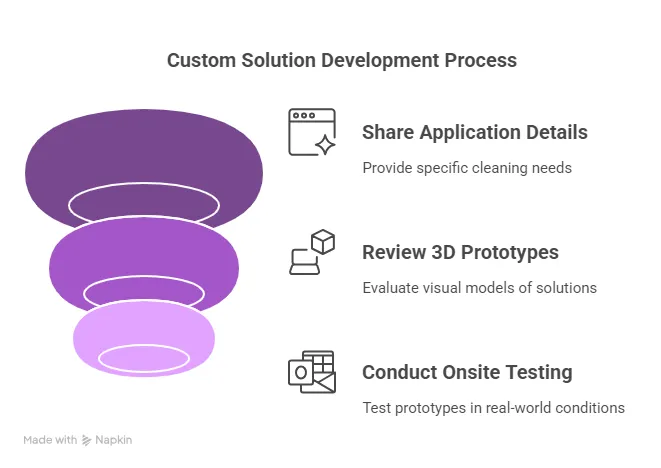
ZEK has engineered vacuums for automotive paint shops and food processing plants, with IP67-rated seals.
10. How Sustainability Practices Impact Your Manufacturer Choice
Eco-conscious manufacturing isn’t just ethical—it future-proofs compliance. Key benchmarks:
-
Materials:
- Recycled plastics (ZEK uses 30% post-consumer resin).
- REACH-compliant non-toxic seals.
-
Energy Efficiency:
- Solar-powered factories (ZEK’s Guangdong facility runs on 60% renewable energy).
- ISO 14001-certified waste management.
-
Packaging:
- Biodegradable foam inserts.
- Minimal plastic wraps.
Demand third-party audits or sustainability reports to verify claims.