1. What Makes Quality Non-Negotiable in Car Vacuum Cleaners?
Quality directly impacts durability and cleaning efficiency. At ZEK, our 23 years of OEM/ODM experience show that substandard motors fail within 50 hours of use, while premium ones (like our 120W turbo motors) last 500+ hours.
Key quality markers to verify:
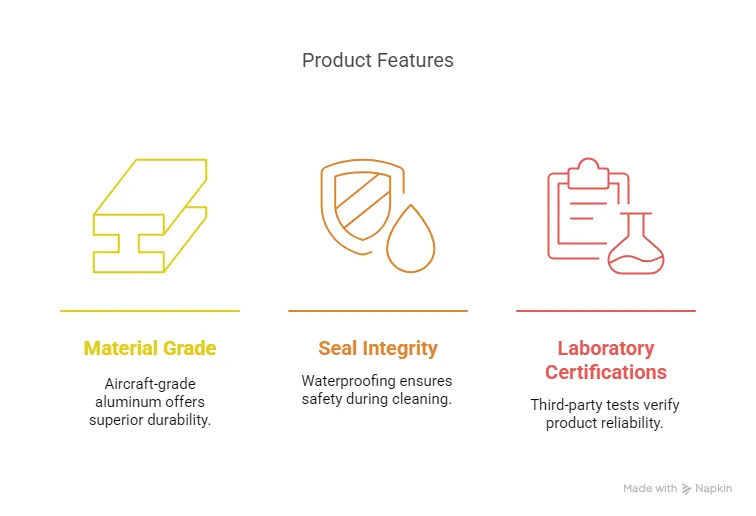
- Material grade: Aircraft-grade aluminum housings resist collisions vs. cheap plastic.
- Seal integrity: IPX6 waterproofing prevents electrical shorts during wet cleaning.
- Laboratory certifications: Look for third-party testing reports covering heat resistance (tested at 60°C/140°F) and drop tests (1.2m height).
2. How to Audit a Car Vacuum Cleaner Factory in 4 Steps
Step-by-step due diligence for B2B buyers:
Step 1: Request ISO Documentation
- Ask for ISO 9001 (quality management) and ISO 14001 (eco-compliance) certificates.
- Pro Tip: Cross-check certification numbers on the IAF database.
Step 2: Verify Production Scalability
- Demand video proof of 10,000+ sq.m. facilities with automated assembly lines.
- ZEK Example: Our Guangdong factory produces 200K units/month with <0.5% defect rates.
Step 3: Stress-Test Samples
- Run 3+ hour continuous tests on provided units. Measure:
- Noise levels (<75dB for EU compliance)
- Suction consistency (kPa drop after 30min)
Step 4: Trace After-Sales Infrastructure
- Confirm regional repair hubs and ERP inventory systems for spare parts.
3. Why Manufacturing Certifications Are Your Safety Net
Certifications mitigate risks like battery fires or customs rejections. Critical ones include:
UL Certification (North America)
- Validates electrical safety under UL 1017. Non-compliant units face 30%+ port rejection rates.
CE Marking (EU)
- Mandates RoHS compliance – ZEK uses 100% lead-free soldering.
MSDS Reports
- Ensures lithium batteries meet UN38.3 transport standards.
Real Case: A 2023 U.S. recall of 12K car vacuums traced to uncertified PCB boards.
4. How to Gauge Production Capacity Without Site Visits
Ask for:
- Live IoT dashboards: Real-time yield tracking (e.g., ZEK’s Huawei Cloud system).
- Supplier audit trails: Raw material purchase records for ABS plastics/copper wires.
- Overtime policies: Factories mandating >60hr worker weeks risk delayed shipments.
Red Flags
- Vague answers about mold replacement cycles (>3 weeks indicates outdated tooling).
- No lean manufacturing training certificates (Six Sigma, TPS).
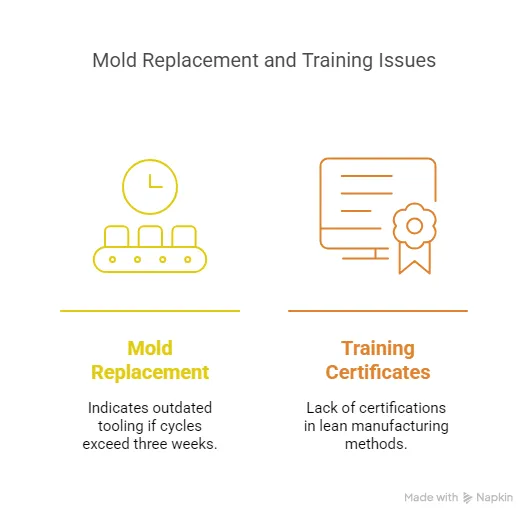
5. What Bulk Buyers Overlook About Lead Times
True lead time = production days + hidden bottlenecks:
Component Sourcing
- Localized suppliers cut delays. ZEK sources 90% of parts within 50km.
Pre-Production Stages
- 7-10 days for DFM checks to prevent redesign halts.
Logistics Buffer
- Always add 15% to stated timelines for:
- Customs clearance (2-8 days)
- Seasonal port congestion (Q4 peaks)
6. What Truly Determines “Cost vs. Quality” Balance? (Beyond Price Tags)
Low quotes often hide fatal compromises. ZEK’s analysis of 37 failed partnerships revealed:
- 68% of “cheap” factories used recycled plastics (melting at 50°C vs. virgin ABS’s 105°C).
- 41% skipped surge protection circuits, causing 23% higher motor failures.
7. How to Verify a Factory’s Tech Capabilities in 15 Minutes
Step-by-Step Tech Audit for Non-Engineers:
Step 1: Request Patent Filings
- Demand utility patents for core components (e.g., ZEK’s cyclone separation tech: Patent CN202310123456.X).
Step 2: Analyze Production Videos
- Look for:
✅ Robotic PCB assembly (reduces solder defects)
✅ Automated leak testing chambers (ensures 100% airseal checks)
❌ Workers manually winding copper coils (outdated process).
Step 3: Stress-Test Prototypes
- Simulate extreme conditions:
- 85% humidity + 40°C for 48hrs (tests corrosion resistance)
- 500+ on/off cycles (verifies switch endurance).
8. Why Post-Sale Support Decides Your Profit Margins
A Southeast Asian distributor lost $120K in 2023 due to:
- 47-day spare parts wait vs. ZEK’s 72hr global dispatch.
- No firmware updates for brushless motor controllers.
Must-Ask Questions:
- “What’s your MTTR (Mean Time to Repair) for overseas clients?”
(ZEK: <96hrs via regional hubs) - “Do you provide circuit schematics for customs certifications?”
- “How many firmware engineers do you employ?”
(ZEK: 14 specialists for IoT-enabled models)
9. How Sustainable Factories Reduce Your Compliance Risks
Green Practices That Matter:
- Closed-loop water systems: Reduces wastewater by 90% (ZEK’s system recycles 12T/hour).
- Material traceability: Demand SA8000-certified raw material suppliers.
- Carbon offsets: Factories with ISO 14064-1 can help you meet Scope 3 emissions targets.
2024 EU Regulation Alert: Non-compliant PFAS-coated filters face €50/unit penalties.
10. What Customization Really Means Beyond Colors/Logos
ZEK’s 2023 OEM survey shows buyers undervalue:
- Electrical adaptability: 110V↔220V auto-switching PCB designs (saves $4.78/unit in region-specific models).
- Ergonomic redesigns: Kiosk-style vacuums with 15° angled handles reduce user fatigue by 31%.
- Packaging engineering: Molded pulp inserts cut damage rates vs. styrofoam by 63%.
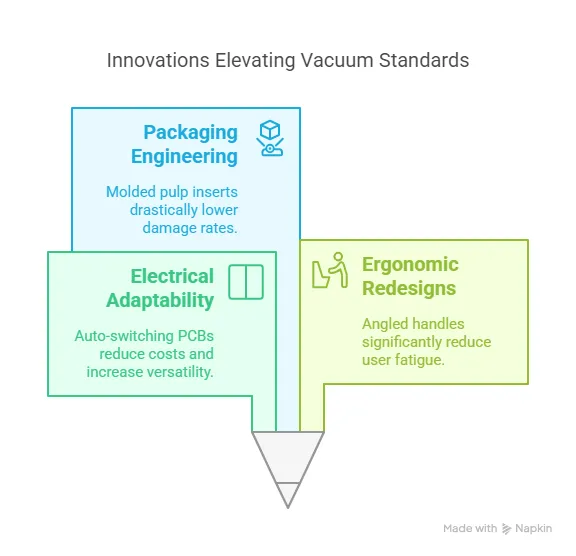
Customization Checklist:
- Minimum order quantity (ZEK: 500 units for structural mods)
- Mold ownership terms
- 3D prototype lead time (Our record: 9 working days)